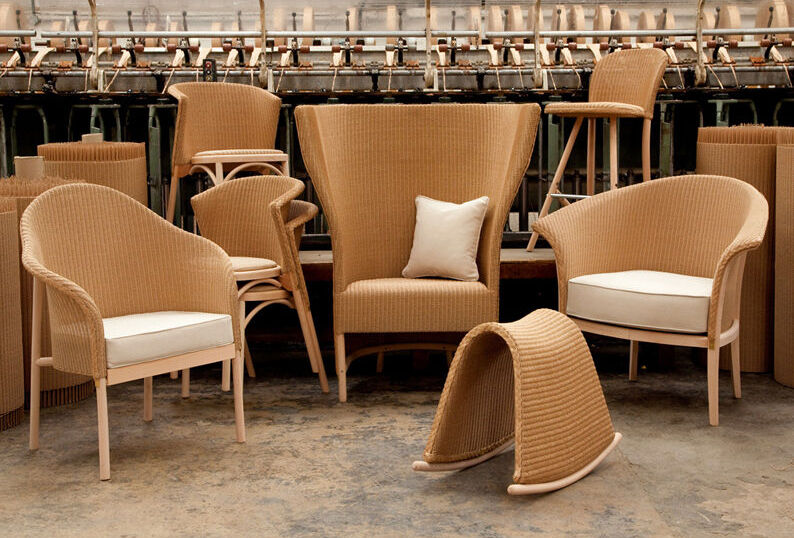
The Lloyd Loom Elves
After working together on various 'bodging' projects, William Warren, Gareth Neal, Carl Clerkin, Amos Marchant and I had the feeling that the hands-on experimental way of working that we had developed in more of a craft setting could be a useful way of fast-tracking the usually long drawn-out process involved in design-for-production. William knew the people at Lloyd Loom and so we got ourselves an invitation to visit their factory in Spalding over a long weekend to brainstorm some new designs based on their existing range of components. (We called this the Lloyd Loom Elves after the childrens' story of the Elves and the Shoemaker.)
The Lloyd Loom 'weave' is fascinating: thin strips of Kraft paper on giant old machines are twisted around wire which is then woven on industrial looms. Wooden frames are simply dowelled together and once the weave is in place and the chair is sealed you have a very strong and lightweight structure.
We came up with thirteen new designs over an intensive three days. Lloyd Loom were very patient with this disruption and even had some of their skilled workforce on hand to help with applying the distinctive Lloyd Loom 'weave'.
In the end it was impossible for them to go ahead with every design and only my chair made it into production. We exhibited the collection at Design Junction where it attracted a lot of interest and was spotted by someone from the John Lewis Partnership. They decided to include my chair as a new piece for their 150-year celebrations. So I drew everything up properly - no drawings are involved in bodging! - and Lloyd Loom began making. Other chairs in the John Lewis 150 Collection were re-workings of classic designs from Ercol, Vitra, and Parker Knoll.
It had been Lloyd Loom's intention to put further pieces from the Elves range into production, but it turned out we had caught them at a bad time. Shortly after, the company was sold and the new owner moved production abroad.